La industria térmica no puede sustituir sus hornos de gas por eléctricos y confía en el hidrógeno verde
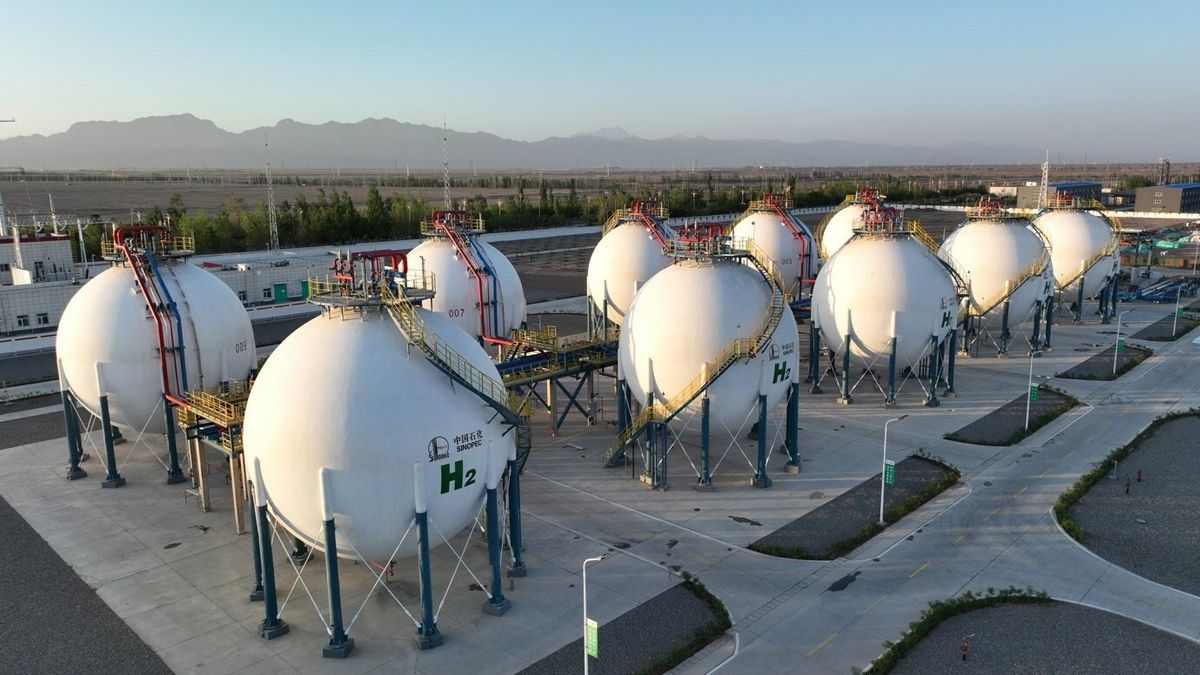
Este miércoles se reunieron en Madrid decenas de fabricantes que consumen grandes cantidades de energía para intercambiar conocimiento sobre la reducción de emisiones a la atmósfera. Todas las empresas presentes se han deshecho ya de su contaminación relacionada con la energía eléctrica, o están camino de ello, pero tuercen el gesto a la hora de hablar del gas natural, el combustible que mueve sus hornos y el que realmente contamina en la industria termointensiva. "Ese es otro tema, va más despacio", resumía uno de los empresarios presentes.
Las más de 40 multinacionales fueron convocadas por Iberdrola en su sede para inaugurar la llamada Alianza Q-Zero, un grupo de empresas que conecta productores de energía con consumidores de calor para reducir las emisiones de CO₂ en la industria. Este sector es uno de los más complejos de descarbonizar, ya que muchas de estas fábricas necesitan alcanzar en sus hornos más de 1.000 grados, y por ahora solo es viable hacerlo con gas o combustibles. La industria térmica consume tanto calor en España como todos los edificios del país, tanto viviendas como oficinas.
Entre los convocados habían grandes consumidores de energía, como cementeras, fabricantes de aluminio, de químicos, papel o plásticos, que queman gas natural en cantidades ingentes en su proceso productivo. Según explicaban sus ejecutivos, consumir electricidad limpia es relativamente sencillo: basta con instalar paneles solares junto a la fábrica o comprar luz renovable a un generador. Sin embargo, todavía no han encontrado una alternativa para los combustibles fósiles en sus hornos, aunque esperan que sea el hidrógeno verde.
"Hacer la transición ahora mismo es complicado. Barajamos alternativas y el hidrógeno verde es una de ellas, pero hace falta inversión, desarrollo tecnológico para aplicarlo en las fábricas y necesitamos un gran volumen", afirma Jorge Fabregat, responsable de Medioambiente de Porcelanosa, fabricante de azulejos. Las azulejeras son unas de las fábricas más intensivas en calor, y necesitan temperaturas de hasta 1.210 grados para hornear la cerámica. Según explica, su compañía se ha centrado hasta ahora en que toda la electricidad sea renovable, pero el 90% de la energía que consume es térmica, es decir, gas natural.
Las alternativas a este combustible —tanto para esta empresa como para el resto— son el biogás y el hidrógeno verde. El primero se captura de desechos orgánicos en descomposición, como vertederos o depuradoras, y el segundo se obtiene separando una partícula de agua por medio de electricidad renovable. Sin embargo, ninguna de las dos opciones se genera en grandes cantidades en España, y hasta que se desarrollen a gran escala son mucho más caras que el gas natural.
En el caso del hidrógeno verde, explican diferentes profesionales de empresas intensivas en calor, se suma que hay que estudiarlo y adaptar la maquinaria a este gas, ya que genera unas condiciones en el interior del horno diferentes al gas, y altera la materia prima que se quiere calentar.
La incertidumbre sobre cuál será el sustituto del gas natural es tan grane que Porcelanosa todavía no ha publicado una hoja de ruta para descarbonizarse. "Hasta que no tengamos un combustible alternativo al gas natural, no vamos a plantear objetivos firmes. Tenemos claro que queremos cumplir con el objetivo de reducir emisiones un 55% en 2030, pero antes hay que ver cómo", apunta Fabregat.
Las emisiones globales crecerán un 1,1% en 2023 y vuelven a alcanzar un nuevo récord
Ver más
Otra de las empresas presentes, el fabricante vasco Tubos Reunidos, relata una situación similar. También tienen hornos de gas para calentar y perforar los el acero inoxidable, que consumen aproximadamente la mitad de la energía de la compañía. El resto es electricidad, que están en proceso de obtener de forma limpia a través de autoconsumo y contratos con terceros. "Para el gas estamos haciendo ensayos con biogás e hidrógeno, pero eso es a largo plazo”, comenta Antón Pipaón, director de Sostenibilidad de la empresa. Además de que no hay una producción suficiente para cubrir su consumo, el precio es todavía muy superior. Han intentado cerrar acuerdos para adquirir pequeñas cantidades de biogás, pero el precio "era cuatro veces superior al gas, o incluso más".
No todas las empresas intensivas en energía reconocieron tener este problema, ya que es una cuestión de cuánta temperatura necesita el proceso productivo de cada industria. En el caso de Bayer, fabricante de medicamentos, están barajando sustituir su caldera de la planta La Falguera (Asturias) por una eléctrica, que funciones con energía solar fotovoltaica con o termosolar, un proceso que se podría realizar hoy mismo. Esto es, porque ellos calientan el vapor a entre 220 y 250 grados. Porcelanosa también ve factible sustituir el gas en su proceso de secado, donde apenas necesita llegar a 180 grados. Para este caso barajan una alternativa por microondas o infrarrojos.
Tanto la cerámica como el acero son dos sectores especialmente difíciles de reducir emisiones, por eso los expertos en energía reclaman que sean estas empresas sean las primeras que reciban el hidrógeno verde o el biogás cuando se produzca, junto con sectores como la aviación o el transporte pesado. Ignacio Sánchez Galán, presidente de Iberdrola, indicó que deshacerse de los combustibles fósiles en la industria traerá "una situación de precios más estables y predecibles para los clientes", y recordó que la importación anual de gas y petróleo a España desde el extranjero cuesta lo mismo que ingresa el país por turismo.